High precision mirror shafts play a crucial role in many high-speed rotating equipment, however, vibration and noise issues not only affect the performance of the equipment, but may also shorten the service life of the shafts. Here are some methods to reduce vibration and noise through optimized design.
Firstly, the structural design of the shaft rod. In the design phase, the length and diameter ratio of the shaft rod should be reasonably determined. Longer shaft rods are more prone to vibration, so it is necessary to minimize the aspect ratio as much as possible based on actual work requirements while meeting functional requirements. Meanwhile, a hollow structure design can be adopted. Hollow shaft rods can effectively reduce mass while ensuring a certain strength, thereby reducing inertial forces and reducing the possibility of vibration.
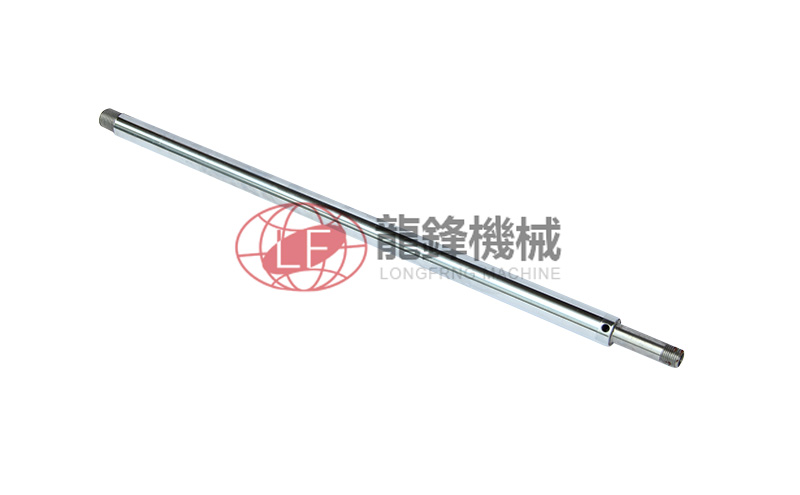
Next is material selection. Choosing materials with high elastic modulus and large damping coefficient is crucial for reducing vibration and noise. For example, some high-performance alloy steels not only have good mechanical properties, but their internal damping can effectively dissipate vibration energy. By precise material ratios and heat treatment processes, the performance of materials can be further optimized to better resist vibration.
Furthermore, there is optimization of surface accuracy. As a mirror axis rod, its surface accuracy directly affects the stability during rotation. A higher surface finish can reduce friction and wear between the mating components, and decrease vibration caused by uneven friction. During the processing, ultra precision grinding and polishing techniques are used to strictly control parameters such as roundness, cylindricity, and surface roughness of the shaft rod, ensuring that the surface of the shaft rod achieves extremely high mirror quality.
Additionally, consider dynamic balancing design. After the manufacturing of the shaft rod is completed, high-precision dynamic balance testing and calibration must be carried out. Even a small mass imbalance can generate enormous centrifugal force during high-speed rotation, leading to vibration and noise. By adding or removing a small amount of material at appropriate positions on the shaft rod, the center of mass of the shaft rod can be aligned with the center of rotation, which can significantly reduce vibration.
Finally, the optimization of bearings and support systems. Choose high-precision, low friction bearings and design the preload force of the bearings reasonably. At the same time, the support structure of the shaft rod is optimized to ensure sufficient stiffness and stability, which can effectively suppress the vibration transmission of the shaft rod and reduce the overall vibration and noise level. Through the optimization design in various aspects mentioned above, the stability of high-precision mirror shaft rods during operation can be effectively improved, and the generation of vibration and noise can be reduced.