I. Core Manufacturing Processes
Material Preparation
Materials: Spring steel, cold-rolled steel (for oil reservoir tubes), or alloy steel (for piston rods). Special components may include nickel, manganese, or chromium alloys to enhance strength and wear resistance.
Key Component Machining
Oil Reservoir Tube:
Cold-rolled steel tube necking/machining → welding bottom cover → welding spring seat/bracket → electrophoretic coating for corrosion resistance.
Critical controls: Weld strength, sealing integrity, dimensional accuracy.
Piston Rod:
45# steel drawing → high-frequency induction surface hardening (improves surface hardness) → chrome plating (micro-crack process) → dehydrogenation → flaw detection.
Surface roughness ≤0.2μm, roundness tolerance ≤0.05mm.
Assembly Process
Valve components (rebound/compression valves) mounted on piston rod → assembly with working cylinder and oil reservoir → vulcanization of main body to aluminum bracket (with top rubber buffer).
Critical steps: Oil seal installation (leak prevention), sealing ring pressing (airtightness testing).
Sealing and Oil Filling
Hydraulic oil filling (bubble-free) → nitrogen charging (0.3–0.6 MPa) → sealing (laser welding or press-fitting).
Performance Testing
Damping Force Test: Low/medium-speed condition force-displacement curve analysis, requiring smooth and consistent curves.
Fatigue Life Test: Simulate >100,000 stroke cycles to detect leaks or abnormal noise.
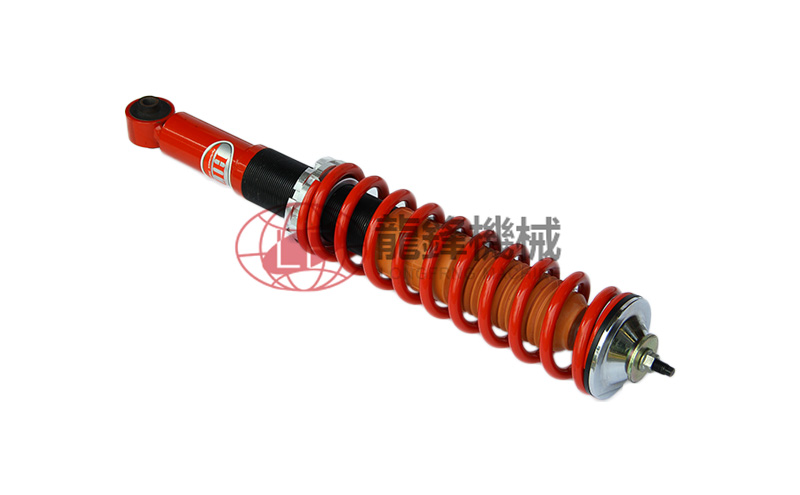
II. Advanced Techniques and Innovations
Cold Extrusion Forming
T-shaped blanks for irregular bushings formed via hydraulic press → multi-station rotary table for drilling, tapping, and milling, improving efficiency by 30%+.
Laser Fusion Welding
Laser welding for piston rod and end cover, reducing manual intervention and thermal deformation risks.
Cleanliness Management
Dust-free assembly environment → ultrasonic cleaning → steam treatment → oil immersion for rust prevention.
III. Critical Quality Metrics
Component/Process | Control Standards | Testing Methods |
Piston Rod Chrome Layer | Micro-crack-free, thickness 20–30μm | Flaw detector + metallography |
Oil Reservoir Sealing | 0.5 MPa pressure retention (no leaks) | Leak tester |
Damping Force Deviation | Rebound/compression force error ≤10% | Force-displacement curve comparison |
IV. Common Failure Modes and Improvements
Oil Leakage:
Seal wear or improper assembly → optimize chrome layer uniformity.
Abnormal Noise:
Valve component jamming → enhance hydraulic oil cleanliness (NAS Class 8).
Fatigue Fracture:
Insufficient piston rod core toughness → refine quenching (retain pearlite in core).
Note: Latest patented technologies (e.g., cold extrusion forming, laser welding) significantly improve manufacturing efficiency and product lifespan.