镜面轴芯的加工是一个要求很高精度的过程,尺寸公差和表面粗糙度的控制尤为关键。尺寸公差决定了轴芯与其它部件的配合精度,而表面粗糙度则直接影响了轴芯的摩擦性能、耐磨性以及寿命。以下是控制这两个参数的主要方法:
尺寸公差控制:
1.精 密测量工具:使用高精度的测量仪器,如激光测微仪、三坐标测量机(CMM),进行尺寸检测,确保每个加工步骤后的尺寸都在公差范围内。
2.数控编程:利用计算机数控(CNC)技术,通过准确的编程来控制机床的运动,减少人为误差,实现自动化加工。
3.温度控制:加工过程中的温度变化会影响材料的膨胀收缩,因此,保持恒定的车间温度有助于控制尺寸稳定性。
4.刀具管理:选用高质量的刀具,并定期检查和更换,避免因刀具磨损造成的尺寸偏差。
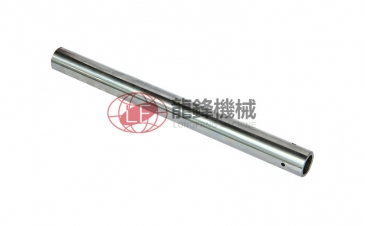
表面粗糙度控制:
1.选择合适刀具:使用锋利且适合材料特性的刀具,减少切削过程中的振动,从而降低表面粗糙度。
2.优化切削参数:调整切削速度、进给率和切深,找到蕞佳组合,以获得平滑的表面。
3.冷却液使用:适当的冷却液可以降低切削区温度,减少热变形,同时清洗切屑,防止二次刮伤。
4.后续精加工:采用研磨、抛光、超精加工等工序,进一步改善表面粗糙度,达到镜面效果。
5.表面处理:通过电镀、化学镀、涂层等表面处理技术,增强表面光洁度和耐腐蚀性。
在整个加工流程中,质量控制是贯穿始终的,每道工序后都应进行严格的检验,以确保蕞终产品符合高精 密镜面轴芯的严格标准。此外,持续改进和工艺创新也是维持和提升加工水平的重要因素。