在镜面轴加工中,要保证加工表面达到高光洁度,需要综合考虑多个因素和技术细节。以下是一些关键点,旨在帮助确保加工表面达到所需的高光洁度:
1. 选择合适的加工方法
镜面加工通常指的是使用特殊的加工技术,如精 密磨削、超精加工或电化学加工等,来获得非常低的表面粗糙度。
外圆磨床可以用来加工轴类零件,通过准确控制磨削过程中的各个参数,可以有效地提升表面光洁度。
2. 使用高质量的工具和材料
刀具材质:选择适合被加工材料的刀具材质至关重要,如硬质合金、陶瓷或金刚石等。
刀具几何形状:合理的刀具几何形状能够减少切削力并降低表面粗糙度。
材料特性:对于不同的材料,可能需要采用不同的加工策略。例如,对于高硬度材料,可能需要采用特殊的切削液或加工方法。
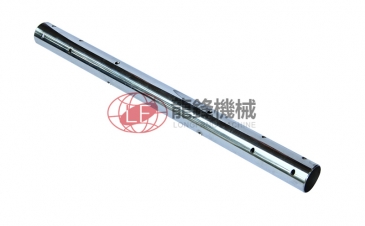
3. 控制加工参数
切削速度:适当的切削速度对于获得良好的表面光洁度非常重要。
进给量:小的进给量有助于减少表面划痕,从而改善光洁度。
切削深度:浅切削深度可以减少振动,有助于保持表面质量。
4. 优化工艺流程
预处理:在进行蕞终的镜面加工之前,进行适当的预处理,比如粗磨或半精磨,以去除表面缺陷。
多道工序:有时需要进行多次加工,每一道工序逐渐减小切削参数,以逐步提高表面质量。
冷却与润滑:使用适当的冷却液和润滑剂可以减少刀具磨损并改善加工效果。
5. 使用精 密检测设备
在线检测:在加工过程中使用高精度的检测设备(如激光测量仪、光学显微镜等)进行实时监控,以便及时调整加工条件。
离线检测:加工完成后进行质量检验,确保达到所需的表面光洁度标准。
6. 消除残余应力
热处理:在加工前后进行适当的热处理,以减少材料内部的残余应力,防止变形。
应力释放:采用一些技术手段,如振动时效或超声波处理,帮助释放材料内部的应力。
7. 环境控制
温度控制:保持稳定的环境温度可以减少因热膨胀引起的误差。
清洁度:确保加工环境的清洁,避免灰尘或杂质污染加工表面。
结论
为了确保镜面轴加工表面达到高光洁度,需要从选择合适的加工方法开始,一直到控制加工参数、优化工艺流程、使用精 密检测设备等多个方面进行细致考量。同时,消除残余应力和严格控制加工环境也是非常重要的环节。通过上述方法的综合运用,可以有效地提高加工表面的光洁度,从而满足高品质应用的需求。