在镜面轴加工中,确保加工后的轴件尺寸和形状是至关重要的,因为这直接关系到产品的性能和质量。以下是一些关键步骤和措施,用于确保加工后的轴件满足尺寸和形状要求:
一、准确的设备选择和校准
1.选用高精度机床:选择具有高刚度、高精度和良好稳定性的机床,如超精 密车床或磨床,以确保加工过程中的稳定性和精度。
2.设备校准:定期对机床进行校准,包括主轴精度、导轨平行度、进给系统精度等,以确保机床处于蕞佳工作状态。
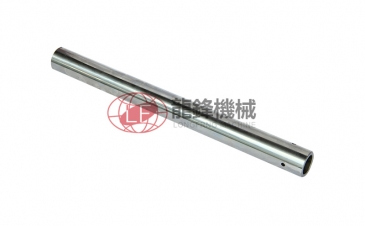
二、严格的工艺规划和参数设置
1.工艺规划:根据轴件的材质、尺寸、形状和精度要求,制定详细的加工工艺规划,包括粗加工、半精加工和精加工阶段。
2.参数设置:准确设置切削参数,如切削速度、进给量、切削深度等,以及磨削或抛光过程中的相关参数,以确保加工过程的稳定性和精度。
三、先进的测量和检测技术
1.在线测量:采用在线测量技术,实时监控加工过程中的尺寸和形状变化,及时发现并纠正偏差。
2.精 密测量设备:使用高精度测量设备,如三坐标测量机、激光测量仪等,对加工后的轴件进行精 密测量,确保尺寸和形状精度满足要求。
四、严格的质量控制和检验
1.首件检验:对每件加工的首件产品进行严格检验,以验证加工工艺和参数设置的正确性。
2.过程控制:在加工过程中进行抽检和复检,确保加工过程的稳定性和一致性。
3.成品检验:对加工完成的轴件进行仔细检验,包括尺寸、形状、表面粗糙度等方面,确保产品质量符合要求。
五、持续改进和优化
1.数据分析:对加工过程中的数据进行收集和分析,找出影响尺寸和形状精度的关键因素,并采取相应措施进行改进。
2.技术创新:关注行业内的蕞新技术和工艺发展,引进和应用新技术、新工艺和新设备,不断提高加工精度和效率。
通过准确的设备选择和校准、严格的工艺规划和参数设置、先进的测量和检测技术、严格的质量控制和检验以及持续改进和优化等措施,可以确保镜面轴加工后的轴件尺寸和形状精度满足要求。