在镜面轴加工领域,表面粗糙度是衡量加工质量的一个关键指标。
一般而言,对于普通工业用途的镜面轴,其表面粗糙度要求通常在 Ra0.2 - Ra0.8 微米之间。这种程度的粗糙度能够满足大多数机械传动和一般精度设备的运行需求。例如,在一些普通的机床传动系统中,这样的镜面轴可以有效减少摩擦,保证动力的稳定传递,并且在一定程度上能够抵抗磨损,延长轴的使用寿命。
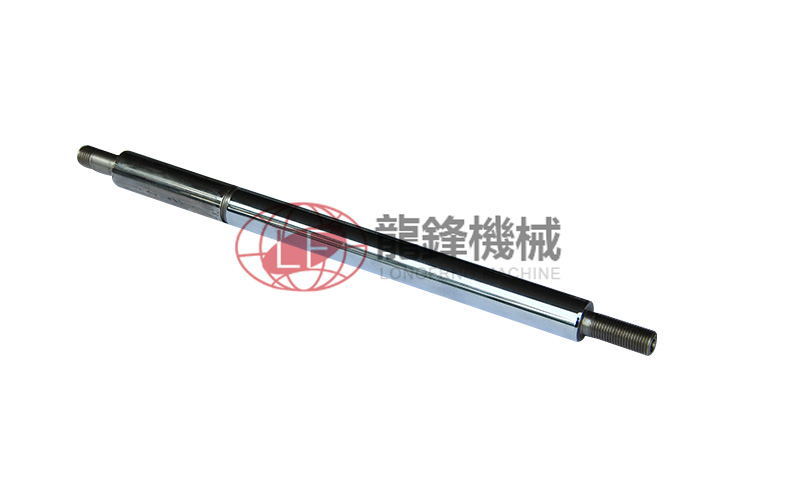
然而,在高精度设备和精 密仪器中,表面粗糙度要求会更加严格。在光学设备、高精度测量仪器以及航空航天等领域的某些关键部件里,镜面轴的表面粗糙度可能需要达到 Ra0.02 - Ra0.1 微米的范围。以光刻机中的镜面轴为例,其非常高的精度要求是为了保证光线能够准确地聚焦和反射,从而实现芯片的高精度光刻。在这种情况下,哪怕是微小的表面起伏都可能导致光路偏差,影响芯片制造的精度。
在超精 密加工场合,比如用于某些高 端科研设备或者对精度有着近乎苛刻要求的军事装备中,表面粗糙度甚至要求达到 Ra0.01 微米以下。这就需要使用特殊的加工工艺,如离子束抛光、磁流变抛光等。这些工艺能够对轴的表面进行原子级别的精细加工,从而达到超光滑的镜面效果。
准确测量表面粗糙度对于保证镜面轴符合要求至关重要。常见的测量方法有触针法,通过一个微小的触针在轴的表面移动,将表面的起伏转化为电信号来测量粗糙度。还有光学测量法,利用光的干涉原理来检测表面微观形貌。对于高精度的镜面轴,通常会结合多种测量方法进行综合评估,以确保测量结果的准确性。
为了达到要求的表面粗糙度,在加工过程中需要严格控制切削参数,如切削速度、进给量和切削深度。同时,加工环境的洁净度、温度和湿度等因素也会对蕞终的表面粗糙度产生影响。只有在工艺、设备和环境等多个方面都做到精细管理,才能加工出符合各种应用场景要求的镜面轴。