在镜面轴加工中,确保轴的圆柱度和直线度等形位公差是至关重要的,这需要从多个环节进行把控。
一、加工设备的精度保证
首先,要选用高精度的机床。机床的导轨直线度、主轴的回转精度等因素直接影响镜面轴的加工精度。例如,使用高精度的磨床,其导轨经过精 密研磨和刮削,能够为加工提供稳定的直线运动基准。定期对机床进行精度检测和校准,通过激光干涉仪等先进设备检测机床的各项精度指标,并及时调整修复,确保机床自身精度符合加工要求。
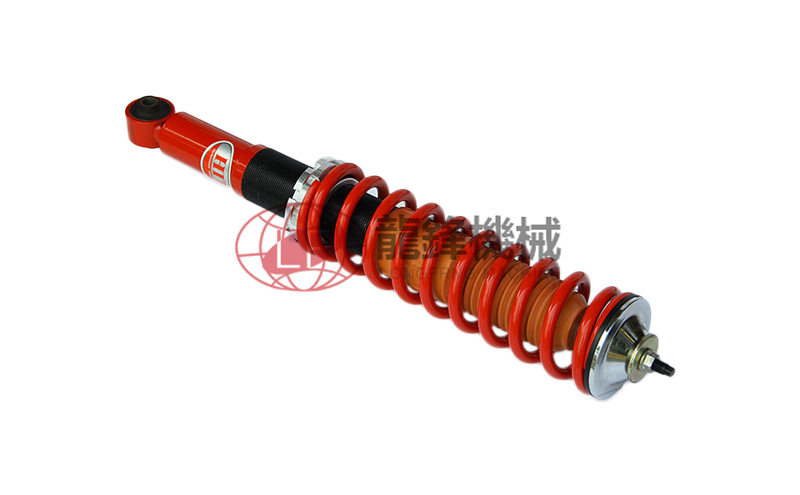
二、合理的加工工艺规划
粗加工阶段,要预留合适的加工余量。余量过大,会导致后续精加工去除余量时产生较大的切削力,使轴发生变形,影响圆柱度和直线度;余量过小,则可能无法完全消除上一道工序留下的缺陷。一般根据轴的尺寸、材质和精度要求等因素,确定合适的粗加工余量。
精加工过程中,采用合适的切削参数。对于切削速度、进给量和切削深度,要根据刀具材料、工件材料以及加工精度要求进行优化。如在磨削镜面轴时,选择适当的砂轮线速度和进给量,能够减小磨削力,避免轴表面因受力不均而出现形状误差。
采用多次走刀的方式。例如在车削或磨削时,通过多次精车或精磨,逐步去除余量,每次走刀的切削深度逐渐减小,使轴的形状精度逐步提高,有效保证圆柱度和直线度。
三、刀具与工装夹具的选择和使用
刀具方面,要确保刀具的锋利度和耐磨性。在加工镜面轴时,使用高质量的刀具材料,如立方氮化硼(CBN)刀具或高精度的砂轮,并且刀具的几何形状要合理设计,能够使切削过程更加平稳。
对于工装夹具,其定位精度和夹紧力的控制十分关键。采用高精度的三爪卡盘或液压卡盘,并设计合理的夹具结构,确保轴在加工过程中定位准确。同时,夹紧力要适中,避免因夹紧力过大导致轴产生弹性变形,影响形位公差。在加工过程中,可以采用一些辅助支撑装置,如中 心架等,增强轴的刚性,减少加工过程中的变形。
四、加工过程中的检测与反馈调整
在加工过程中,要使用高精度的检测仪器,如圆度仪、轮廓仪等,对轴的圆柱度和直线度进行实时检测。一旦发现精度偏差超出允许范围,及时调整加工参数或刀具路径。例如,通过数控系统中的补偿功能,对刀具的位置进行微调,修正加工误差,从而确保轴的形位公差始终处于合格范围内。