在镜面轴加工过程中,加工应力集中导致的轴体变形是一个关键问题,以下是几种有效的解决方法:
一、优化加工工艺参数
合理的切削参数对于减少应力集中至关重要。在切削速度方面,不能过高也不能过低。如果切削速度过快,会产生大量的切削热,导致材料局部膨胀和收缩,从而产生应力。例如,对于钢材的镜面轴加工,切削速度一般控制在合适的范围内,如 100 - 200m/min。进给量也需要精细调整,过小的进给量会使刀具在同一位置停留时间过长,增加应力,而合适的进给量可以使切削力均匀分布,减少应力集中。通常,进给量可以根据轴的直径和材料等因素设定在 0.05 - 0.15mm/r 之间。切削深度同样需要谨慎控制,应采用多次小切深的方式,避免单次切削深度过大而引起应力突变。
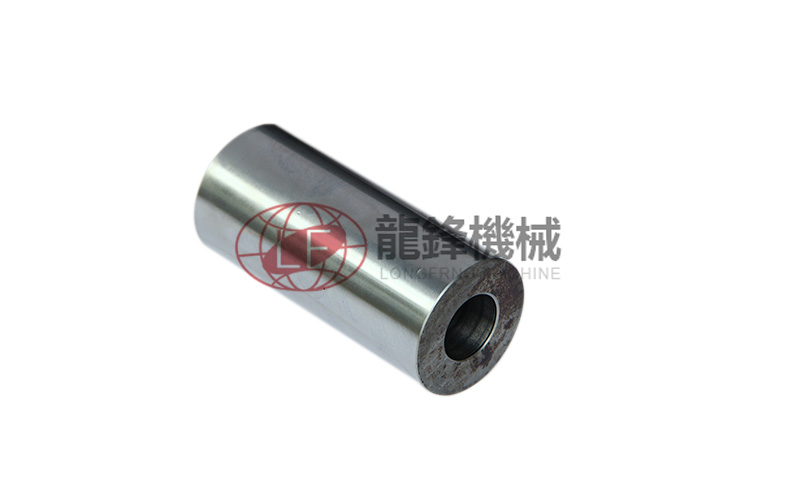
二、采用合适的刀具和切削方式
刀具的几何形状和材质对加工应力有显著影响。选择具有合适刃口半径的刀具,刃口半径过大容易产生较大的切削力,进而导致应力集中;刃口半径过小则刀具容易磨损,影响加工质量。例如,使用涂层硬质合金刀具,涂层可以降低刀具与工件之间的摩擦系数,减少切削热的产生。在切削方式上,采用顺铣方式相较于逆铣能够更好地减少加工应力。顺铣时,切削力的方向有助于工件的压紧,而逆铣会使工件有抬起的趋势,增加应力产生的可能性。
三、进行有效的热处理和时效处理
在加工前或加工过程中对轴体材料进行适当的热处理是减少应力集中的有效措施。例如,对金属材料进行退火处理,可以消除材料内部的残余应力。退火温度和时间需要根据材料的种类和性能要求进行准确控制。对于一些高精度的镜面轴,在粗加工后还可以进行时效处理。时效处理可以使材料内部的组织结构更加稳定,进一步释放加工过程中产生的残余应力。比如,铝合金镜面轴在粗加工后,在一定的温度(如 150 - 200℃)下进行时效处理数小时,能够有效减少后续精加工时的应力变形。
四、合理的装夹方式
正确的装夹方式可以避免因装夹力过大而产生应力集中。在装夹时,要确保装夹点的分布均匀,并且装夹力适中。可以采用弹性装夹装置,如使用液压卡盘等,它能够根据轴体的尺寸和形状自动调整装夹力,使装夹力均匀地作用在轴体上。同时,对于细长的镜面轴,可以采用辅助支撑装置,如中 心架等,来减少因自身重力和切削力引起的变形和应力集中。