一、核心加工流程
材料準備
選用彈簧鋼、冷軋鋼(貯油缸)或合金鋼(活塞桿),部分特殊部件加入鎳、錳、鉻等合金元素提升強度與耐磨性。
核心零件加工
貯油缸:
冷軋鋼管縮頸/機加→焊接底蓋→彈簧盤/支架焊接→電泳塗裝防腐。
關鍵控制點:焊接強度、密封性、裝配尺寸精度。
活塞桿:
45#鋼拉拔→高頻感應表面淬火(表層硬度提升)→鍍鉻(微裂紋工藝)→去氫處理→探傷檢測。
表面粗糙度需≤0.2μm,圓跳動公差≤0.05mm。
組裝工藝
閥系元件(復原閥、壓縮閥)裝配至活塞桿→與工作缸、貯油缸組裝→硫化主體與鋁支架連接(需頂膠緩衝)。
關鍵環節:油封安裝(防漏油)、密封圈壓裝(氣密性檢測)。
密封與注油
專用液壓油灌裝(無氣泡)→充氮氣(0.3-0.6MPa)→封口(雷射焊接或壓裝)。
性能測試
阻尼力檢測:低速/中速工況下示功圖測試,要求曲線連續飽滿。
疲勞壽命測試:模擬10萬次以上行程循環,檢測洩漏與異響。
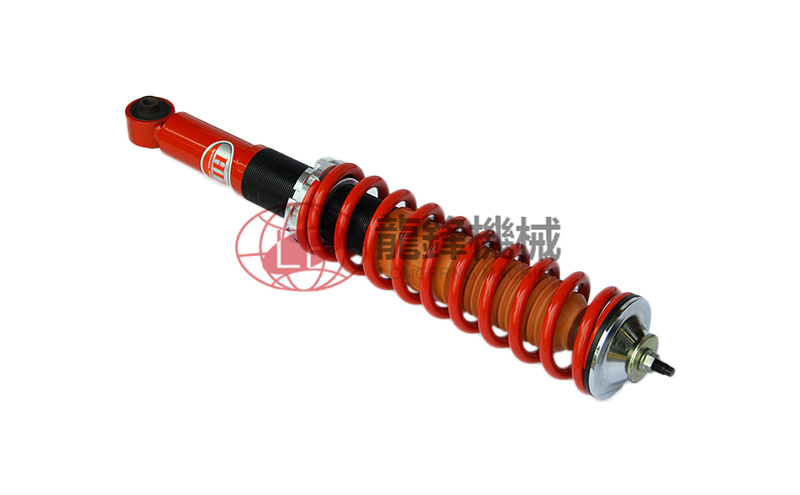
二、特殊工藝與創新技術
冷擠壓成型
異型襯套採用油壓機冷擠壓T型坯料→多工位迴轉台同步完成鑽孔、攻牙、銑邊,提升效率30%以上。
雷射熔焊技術
活塞桿與端蓋採用雷射焊接,減少人工干預,降低熱變形風險。
清潔度管理
裝配全程無塵環境,零件超音波清洗→蒸氣處理→浸油防鏽。
三、關鍵質量指標
部件/工藝 | 控制標準
| 檢測方法 |
活塞桿鍍鉻層 | 無微裂紋,厚度20-30μm | 探傷儀+金相分析 |
貯油缸密封性 | 0.5MPa氣壓保壓無洩漏 | 試漏儀 |
阻尼力偏差 | 復原/壓縮力誤差≤10% | 示功圖對比 |
四、典型失效模式與改進方向
漏油:
油封磨損或裝配不當→優化鍍鉻層均勻性。
異響:
閥系元件卡滯→提升液壓油清潔度(NAS 8級)。
疲勞斷裂:
活塞桿芯部韌性不足→改進淬火工藝(芯部保留珠光體)。
註:最新專利技術(如冷擠壓成型、雷射熔焊)可顯著提升加工效率與產品壽命。